Note: Always use new piston rings when reassembling the engine.
2. Using a piston ring installer, carefully remove the rings from the pistons. Do not notch or gouge the piston in the process. If you do not have such a tool, install the piston rings using three old feeler gauges or similar thin metal strips. Carefully spread the ends of the upper ring and insert the vanes between the ring and the piston, then release the ring over the vanes and remove it. Repeat with the other two rings, using the paddles to prevent the bottom rings from falling into the top grooves. Since the rings must be replaced, it does not matter if they are accidentally broken, but the experience gained from successful removal will be invaluable when new rings have to be installed.
3. Clean all carbon deposits from the top of the piston. A wire brush or fine sandpaper can be used for this. Do not, under any circumstances, use a wire brush installed in an electric drill to remove deposits from the pistons. The material of the piston is soft and easily destroyed by a wire brush.
4. Using a special tool for cleaning the grooves under the piston rings, remove all deposits from the grooves. If the tool is not available, a piece cut from the old ring will serve as a replacement. Be very careful not to remove metal or score or scratch the walls of the annular grooves (photo). Put on protective gloves - a piece of the old ring has sharp edges.
![]() Use a piece of the old ring to carefully remove carbon deposits from the ring grooves | ![]() If possible, clean the annular groove with a special tool |
5. After removing carbon deposits, clean the piston/connecting rod assembly with solvent and dry it thoroughly. Make sure that return lubrication holes in the walls of the annular grooves are not clogged (photo).
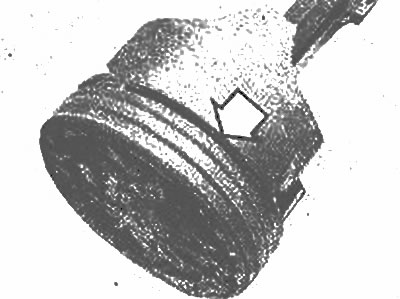
Make sure the oil return holes of the oil ring grooves are not clogged
6. If the pistons are not damaged or excessively worn, and if the cylinder block does not need regrinding, there is no need to replace the pistons. Usually the lateral bearing surface of the piston wears out and there is a slight play of the upper ring in the groove. It is recommended to install new piston rings.
7. Carefully inspect the skirt, as well as the location of the piston pins and the annular grooves of each piston for cracks.
8. Inspect the thrust surface of the skirts for scratches and abrasions, and the piston heads for burnt spots. If the skirt is frayed or scratched, the engine may have overheated, which could be caused by problems with the cooling or lubrication system, or improper ignition timing. Carefully check the cooling and lubrication systems. The presence of burnt recesses in the piston head indicates incorrect adjustment of the ignition timing. Scorched edges of the piston head are usually indicative of detonation. If such damage is found, its causes must be identified and eliminated, otherwise the damage will occur again.
9. Piston corrosion (usually dotted) indicates that coolant is entering the combustion chamber and/or crankcase. The cause must also be identified and corrected.
10. Measure the piston ring backlash by placing a new piston ring in each of the grooves and inserting a feeler gauge between the ring and the ring groove wall (photo). Measure the clearance at three or four places on each groove. Be sure to install the appropriate ring in each groove - they are different. If the side clearance is greater than specified in Specifications, replace the pistons.
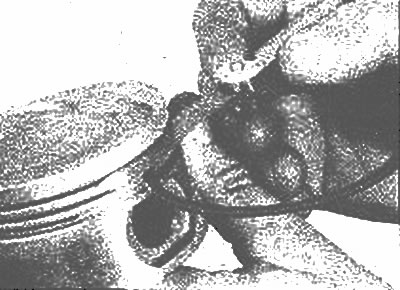
Insert the ring into the groove, then measure the annular gap with a feeler gauge
11. Check the clearance between the piston and the cylinder wall by measuring the cylinder bore diameter and the piston diameter (see chapter 14). Do not confuse pistons and cylinders, they are a matched pair. Measure the piston across the skirt (photo). Subtract the piston diameter from the cylinder bore diameter to calculate the clearance. If it is more than indicated in Specifications, the cylinder block must be bored and new pistons and rings installed. (The clearance between the piston and the cylinder wall can be measured (less accurate) using a feeler gauge, by installing the piston without rings in the cylinder bore.)
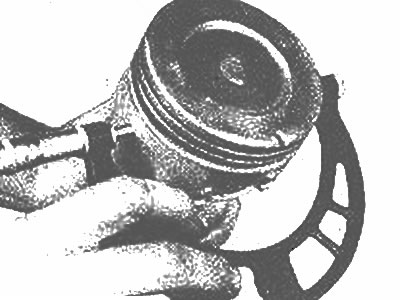
Measure the piston diameter at 90°from the piston pin hole
12. Check up lateral backlash of an axis of a rotary finger, turning the piston and a rod in opposite directions. Any noticeable play indicates excessive wear. In this case, the connecting rod/piston bores must be reground and new piston pins installed - contact a specialist.
13. If it is necessary to remove the pistons from the connecting rods, for example to replace the pistons or piston pins, contact a workshop. At the same time, it is recommended to check the connecting rods for deformation (the station has the appropriate equipment).
14. Examine rods on cracks and other damages. Temporarily remove the connecting rod caps, remove the bearing shells, wipe the working surfaces of the connecting rods and caps and inspect them for notches and scratches. Replace old bearings, install caps and tighten nuts by hand.