Examination
1. The crankshaft position sensor determines the moment and order of fuel injection and ignition in the engine cylinders. The same sensor also measures the crankshaft speed. On models of early releases, the sensor was located in the ignition distributor. On models of later releases, in addition to the sensor, another sensor is installed in the distributor - next to the crankshaft pulley. On engines manufactured since 1998, equipped with an ignition system without a distributor, only one crankshaft position sensor remained - next to the pulley. A sensor malfunction is detected by the diagnostic system and the corresponding code appears in the system memory (see paragraph 2).
Sensor in the ignition distributor (sensor #1)
2. Remove the ignition distributor from the engine and reconnect the larger of the two connectors.
Caution: Do not connect the 3-pin connector as this will cause the coil to spark during the test below.
Also disconnect the wiring connector to the injectors so that the injectors will not work during the upcoming test.
3. Measure the voltage at the CKP1 pin on the outside of the connector (connect the second probe of the voltmeter to the GRD contact) (pic. 8.3, a, b). With the ignition on, turn the distributor rotor by hand and observe the voltage. For one revolution of the rotor, the voltmeter should register one pulse per cylinder. In other words, for every rotation of the rotor, there should be four pulses on a 4-cylinder engine, or 6 pulses on a V-engine. The speed of rotation of the rotor does not matter.
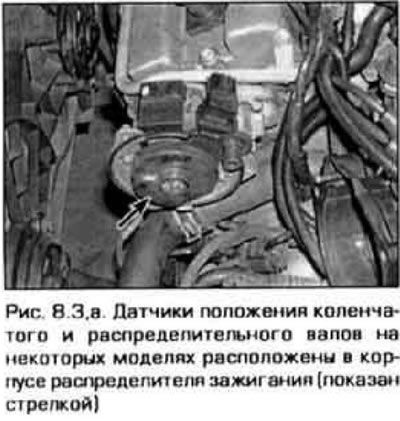
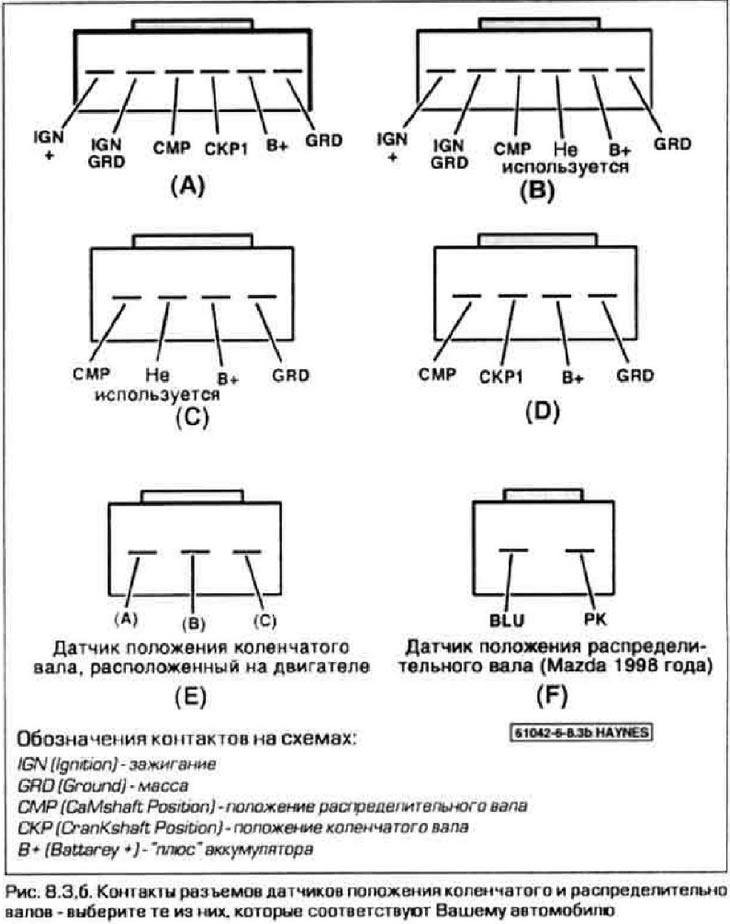
4. If the test does not give the specified results, replace the sensor. The sensor may not be supplied as a separate spare part. In this case, you will have to replace the entire distributor assembly (see chapter 5). Check this question with the spare parts store.
Sensor located on the engine (sensor #2)
5. Measure the gap between the sensor tip and its gear on the crankshaft (pic. 8 5). It should be within 0.5-1.5 mm. The gap is not adjustable and if it is outside the specified limits, replace the sensor or bracket (if the model provides for removal of the bracket).
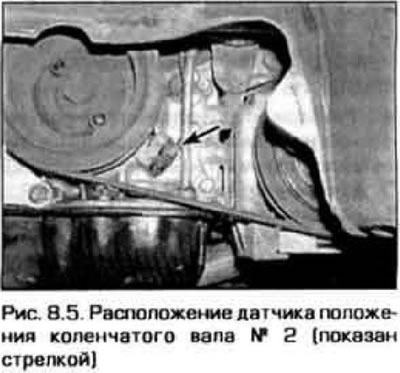
6. To check the sensor, disconnect its electrical connector and measure the resistance between pins A and B (see fig. 8.3b). The resistance should be approximately 550 ohms (in the range from 520 to 580 ohms). If it is not, replace the sensor.
Replacement (sensor #2)
9. Disconnect the negative cable from the battery.
Caution: If your vehicle's audio system is equipped with an anti-theft protection, make sure you know the unlock code before disconnecting the battery.
10. Separate an electric socket of the gauge and release conducting from collars and ties.
11. Turn out bolts of fastening of the gauge and remove it from the engine.
12. Installation is carried out in reverse order. Check the gap between the tip and the sensor wheel and make sure that it is within the limits specified in step 5.