2. Remove the cover of the lower head of the first connecting rod (rods must be numbered). Remove the old bearings and clean the bores of the lower connecting rod head and its cap with a clean, lint-free cloth. Surfaces must be perfectly clean.
Checking the clearances in the bearings of the lower heads of the connecting rods
3. Wipe the outside of the upper connecting rod bearing and insert the connecting rod bore. Make sure that the lug of the liner fits into the cutout on the connecting rod, and the oil holes match. Be careful not to scratch the working surface of the liner and do not drive the liner into the bore. Do not use oil at this stage.
4. Wipe the outer surface of the second half of the bearing and insert it into the connecting rod head cover. Align the protrusion of the liner with the cutout and, as before, do not lubricate anything. It is important that when assembling the connecting rod bearing, there is nothing superfluous between the bore of the lower head and the liners - neither dirt nor oil.
5. Turn the piston rings so that their locks are in the position shown in fig. 26.5.
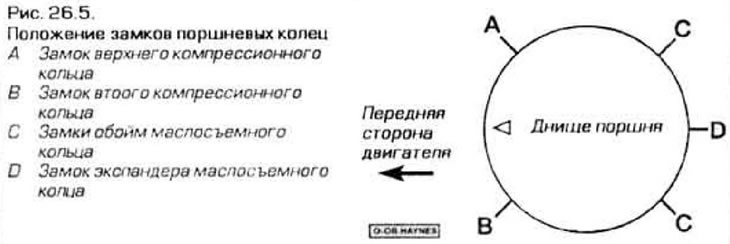
6. Turn the engine on the stand with the crankshaft down.
7. Lubricate the rings and piston with engine oil and install a ring clamp on the piston to compress the rings. Leave free 10-15 mm skirt to center the piston relative to the cylinder. The rings must be compressed so that they are flush with the surface of the piston.
8. Turn the crankshaft so that the crank of the first cylinder is in the BDC position. Lubricate the cylinder mirror with engine oil.
9. Insert the piston so that its front mark is facing the front of the engine and push the piston into the cylinder until the collar stops in the block. On 4-cylinder engines, the front mark "F" (front) located in a recess next to the piston pin. On V-shaped engines, there is a mark in the same place "A" for the right block and "I" - for the left one, which should also be turned towards the front side of the engine during installation.
10. Tap the tie until it rests on the surface of the block all the way around.
11. Gently tapping with a wooden hammer handle under the piston niche (pic. 26.11), push it down while adjusting the bottom end of the connecting rod so that it rests on the crankshaft journal. The piston rings will try to pop out of their grooves as they move from the yoke to the cylinder, so keep the yoke pressed against the block at all times, not allowing any gaps to form between them. Work slowly and if unusual resistance occurs, stop immediately. Look for the cause of the increased resistance before proceeding.
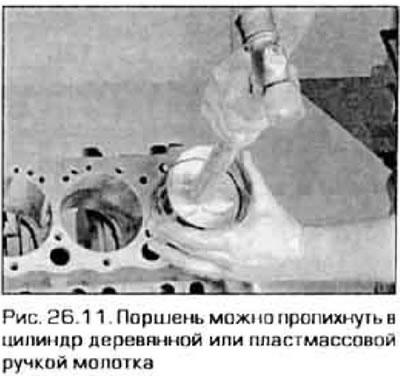
Attention! Under no circumstances try to push the piston by force - at best, you risk breaking the ring, and at worst, damaging the piston or cylinder.
12. Before you finally complete the assembly of the lower head of the connecting rod, you should measure the clearance in the connecting rod bearing.
13. Cut a piece of plastic rod of suitable length from the kit "plastic probe" and carefully place it on the crankpin along the axis of the shaft (pic. 26.13).
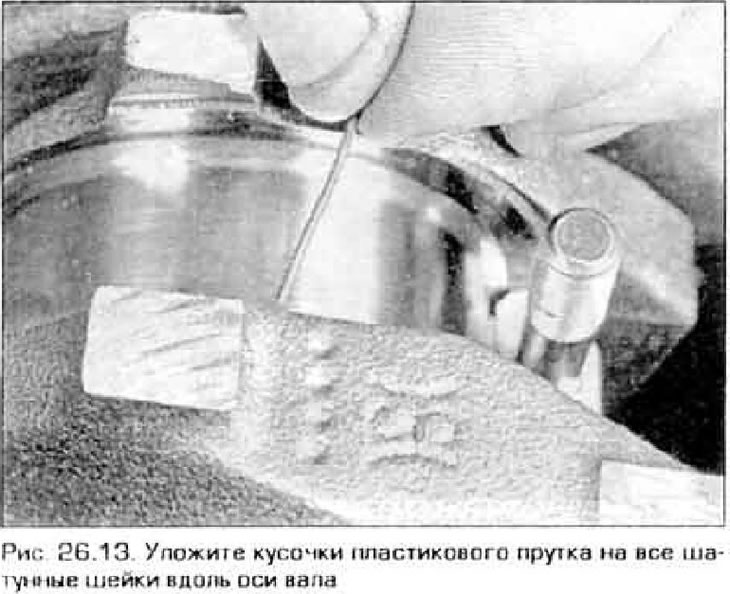
14. Wipe the inside of the bushing in the bearing cap and replace the cap. Make sure the mark on the cap is on the same side as the mark on the connecting rod.
15. Lightly grease the bottom surfaces of the mounting nuts, thread them onto the bolts and tighten in three stages to the torque specified in Technical Data this chapter. For proper tightening, make sure that the socket does not pinch between the nut and the connecting rod cap. The gap here is quite small and you will need a thin wall head. Do not turn the crankshaft during this operation.
16. Turn away nuts and remove a cover, being careful not to displace a plastic bar.
17. Compare the width of the flattened plastic bar with the template and read the gap from it (pic. 26.17). Compare the resulting value with technical data.
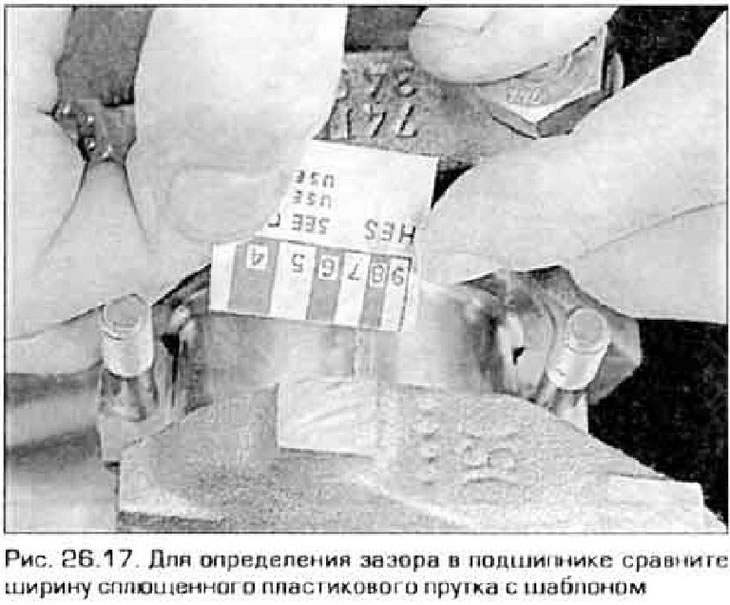
18. Inconsistency with the recommended gap may mean that the liners are the wrong size (in this case they need to be changed). Before deciding to replace bearings, make sure no dirt or oil has entered between the bearings and bores in the connecting rods or bearing caps during measurement. If "plastic probe" noticeably wider on one side than on the other, this means that the crankpin has a taper (see paragraph 19).
Final installation of connecting rods
19. Carefully remove the remaining plastic from the necks or from the liners. Do not scratch the bearing surfaces, scrape the plastic with your fingernail or credit card.
20. Make sure the bearing surfaces are absolutely clean, then lubricate them with molybdenum or engine build grease - this will require you to push the piston a little into the cylinder to get to the top bearing surface. In order not to scratch the neck of the shaft, put protective tubes on the connecting rod bolts.
21. After lubricating the liners, lower the connecting rod bottom head back into place, remove the protective tubes from the bolts, reinstall the cover and tighten it with nuts until the force specified technical data.
22. Repeat this procedure with the rest of the connecting rods.
23. It is important to remember the following:
- A) The bearing and bore surfaces of the connecting rod and cap must be absolutely clean before assembly.
- b) Inserting the piston into the cylinder. You must be sure that you are inserting the correct piston.
- V) The mark on the piston must face the front of the engine.
- G) Lubricate the cylinder walls with clean oil only.
- d) Lubricate bearings and shaft journals only at final assembly, after checking clearances.
24. After the final installation of all connecting rods, turn the crankshaft several times by hand to make sure there are no jams.
25. Followed the operation - checking the axial play of the lower head on the crank - see paragraph 13.
26.Compare the measured end play with technical data. If before the bulkhead it did not go beyond the permissible limits, and if you did not change the connecting rods, it should remain the same. If the connecting rods or crankshaft were replaced, then the play could go beyond the allowable limits. In this case, the connecting rods will have to be removed and given to the workshop for machining.