2. Install the final drive gear.
A) Apply sealant to the contact surfaces of the driven gear and differential housing.
b) Install the driven gear and tighten the bolts.
- Tightening torque - 69 - 83 Nm
3. Using a press and a mandrel, press the side bearings onto the differential case.
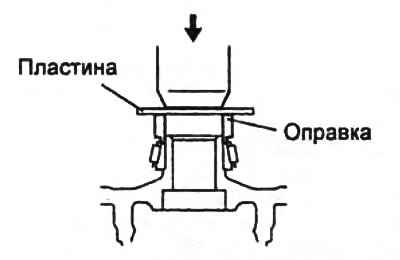
4. Using a press and a drift, press the front bearing outer race into the gear housing.
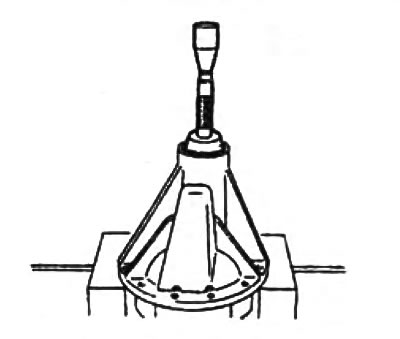
5. Using a press and a special drift, press the rear bearing outer race into the gearbox housing.
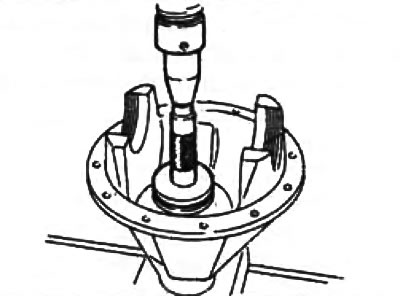
6. Height adjustment of pinion.
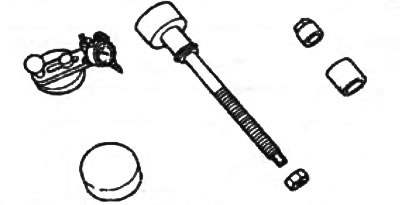
Adjustment tools
A) Fit the rear bearing but the special tool and install the tool together with the rear bearing into the gearbox housing.
b) Install the front bearing and washer with the special tool. Tighten the tool nut until it can be rotated by hand.
Attention: Do not install shims.
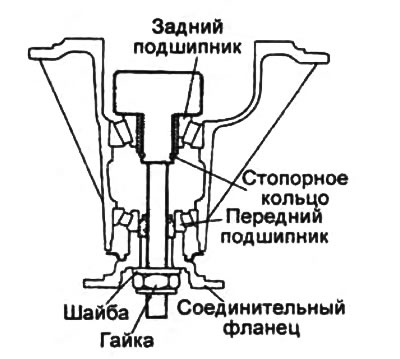
V) Lay the special tool with a dial indicator on a flat surface and set the indicator needle to zero.
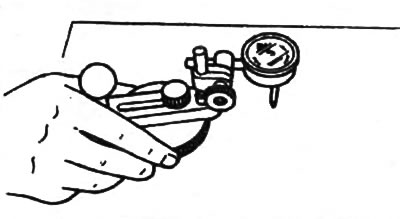
G) Install the indicator tool. the cook is shown in the figure.
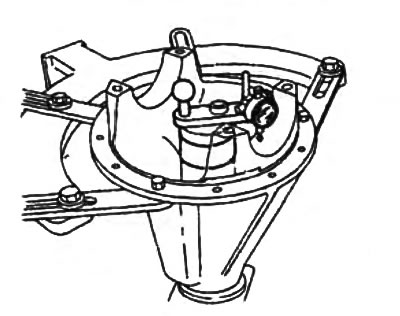
d) Install the measuring tip of the indicator on the place of the gearbox housing where the beds of the side bearings are located. Measure the positions of the lowest points of the beds of the right and left bearings.
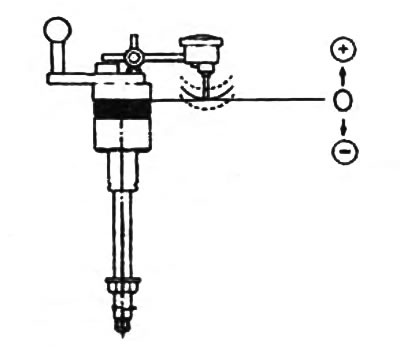
e) Add up the values (right and left), defined in paragraph "d", and divide the resulting amount by 2.
From the result, subtract the number printed on the end of the drive gear and divided by 100 (the absence of a number corresponds to the value zero).
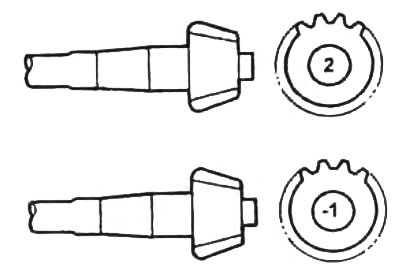
The meaning of the marks on the drive gear:
- "2" — + 0.02 mm
- "-1" — -0.01 mm
Example:
- The value of the two measured values is 0.18 and 0.26 mm and the number on the drive gear is 2. (0,18 + 0,26) /2 - 2/100 - 0.20. The adjustment index value for this pinion and gear case set is 0.20 mm.
- Choose shims of this thickness and install them between the bearing housing and the gearbox housing.
Note:
- select the thickness of the set of shims with an accuracy of 0±0.03 mm;
- no more than five pads can be used.
Note: See the table for the correspondence between the spacer thickness and ID number "Thickness of shims".
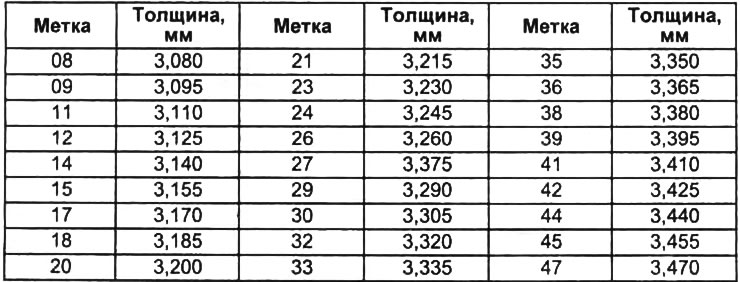
7. Using a press and special mandrels, press the rear bearing onto the pinion gear.
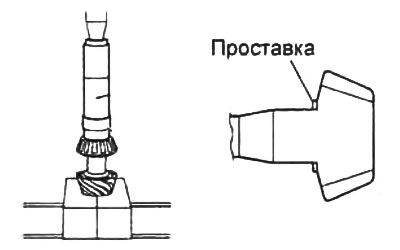
8. Adjusting the preload of the pinion bearings.
Attention: do not install the oil seal.
A) Install pinion, new spacer, connecting flange, washer, and new adjusting nut into bearing housing. Temporarily tighten the adjusting nut.
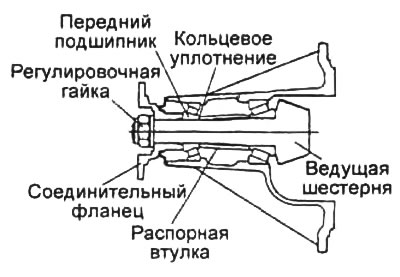
b) To install the bearings, turn the connecting flange by hand.
V) To achieve the set bearing preload, while holding the connecting flange with a special tool, tighten the adjusting nut to the lower torque value.
- Tightening torque - 128 - 284 Nm
- Pinion bearing preload - 1.28 - 1.76 Nm
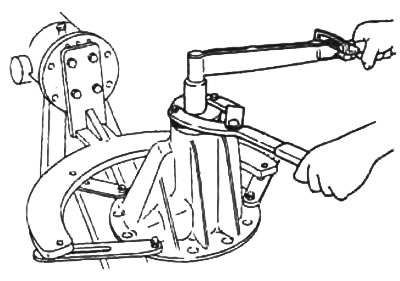
Note: If the preload cannot be achieved, disassemble the assembly, re-adjust the pinion height, and re-adjust the preload with a new spacer.
d) Remove the adjusting washer and connecting flange.
9. Using a drift and a hammer, fully press the gland into the body.
Note: Lubricate the sealing lip of the oil seal with gear oil.
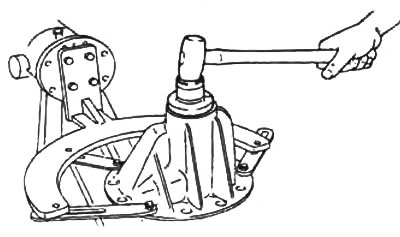
10. Install the adjusting nuts into the gearbox housing.
Note:
- install the adjusting nuts on the side from which they were removed;
- Align the threads on the adjusting nut and the gearbox housing.
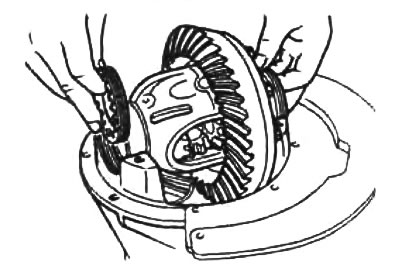
11. Install the bearing caps and temporarily tighten the bolts.
Note: Align the threads on the bearing cap and the adjusting nut.
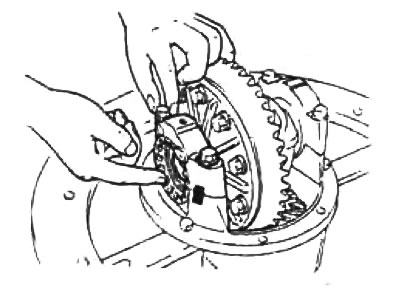
12. Backlash adjustment.
A) Turning the driven gear of the final drive, alternately, using a special tool, tighten the right and left adjusting nuts to reduce the play.
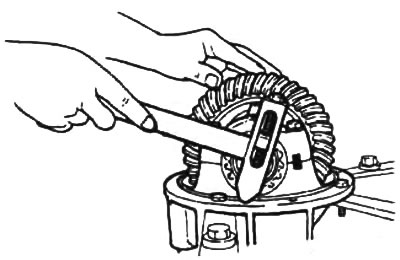
b) Place four marks on the driven gear at 90°intervals.
V) Install the dial indicator on the gearbox housing so that its pin contacts at a right angle with one of the teeth of the driven gear.
G) While holding the connecting flange, turn the driven gear to measure the backlash at the four marked positions.
Make sure that the play in one of the positions corresponds to the established norm, and in other positions does not differ from the measured value by less than 0.07 mm.
Note: The various backlash measurements must fall between the minimum and maximum backlash limits.
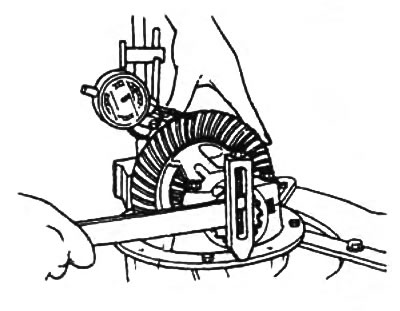
- Standard backlash values - 0.09 - 0.11 mm
- The maximum difference between backlashes is 0.07 mm
Note: To adjust, loosen the adjusting nut on one side and tighten the adjusting nut exactly the same amount on the other side.
d) If the backlash value does not fit within the established norms, reduce it by turning both adjusting nuts in turn.
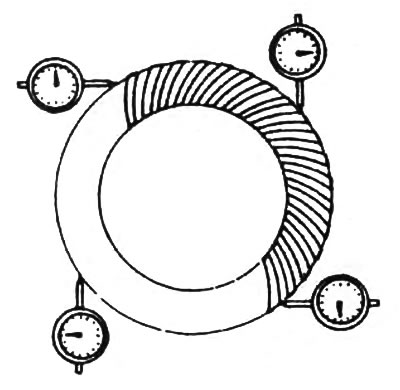
Note: tighten the adjusting nuts to the same angle if the measured distance between the projections on the bearing caps is less than the specification and unscrew the adjusting nuts if the measured distance is greater than the specification.
e) Using a micrometer, measure the distance "L" between the lugs on the bearing caps as shown.
- Distance norm "L" - 204.5 mm
![]() | ![]() |
and) After adjusting the distance "L", recheck the play.
h) tighten the side bearing cap bolts.
13. Checking and adjusting the contact patch in the final drive.
A) Apply a thin coat of red lead to both surfaces of the 6 to 8 teeth of the final drive gear.
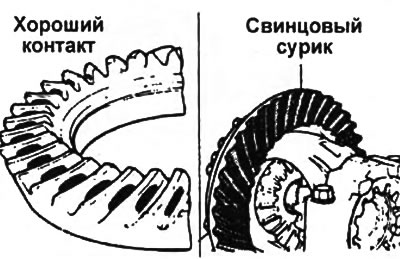
b) Rotate the drive gear back and forth several times and check the contact of the teeth.
V) If the contact is good, remove the red lead applied for testing.
G) If the contact is poor, adjust the pinion height and then adjust the play.
- Contact along the inside of the tooth and along the base of the tooth.
Select a set of shims so as to move the drive gear along its axis from the driven gear.
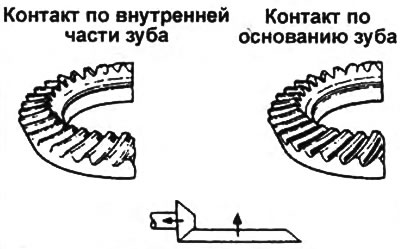
- Contact along the outer part of the tooth and along the upper edge of the tooth.
Select a set of shims so as to move the drive gear along the xX axis to the driven gear.
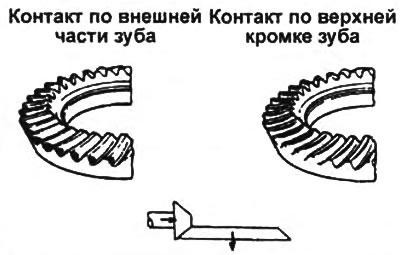
14. Final tighten the bearing cap bolts.
- Tightening torque - 73 - 106 Nm
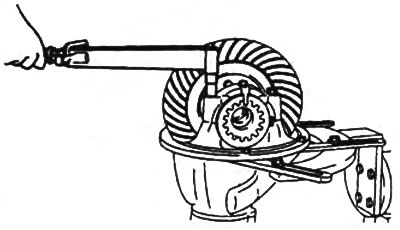
15. Using a mandrel and a hammer, install the side oil seal.
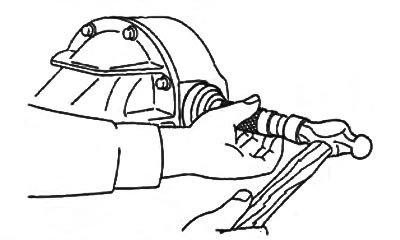